An RDF Alternative Fuel Preparation System For A Cement Company in Sichuan Province is on stable operation!
In October 2024, A cement company in Sichuan province adopted a Harden RDF alternative preparation system with advanced and multiple solid waste processing technologies, to achieve the continuous and steady operation of RDF alternative fuels processing for cement kiln.
As a traditional high energy-consuming industry, the cement industry’s fuel and power costs have accounted for more than 50% of its production cost.
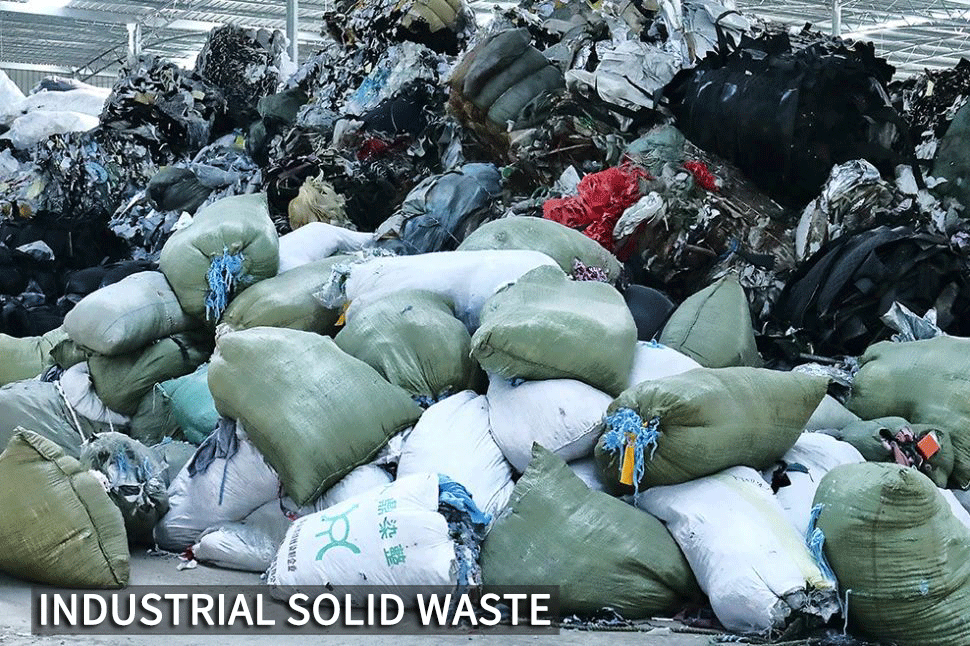
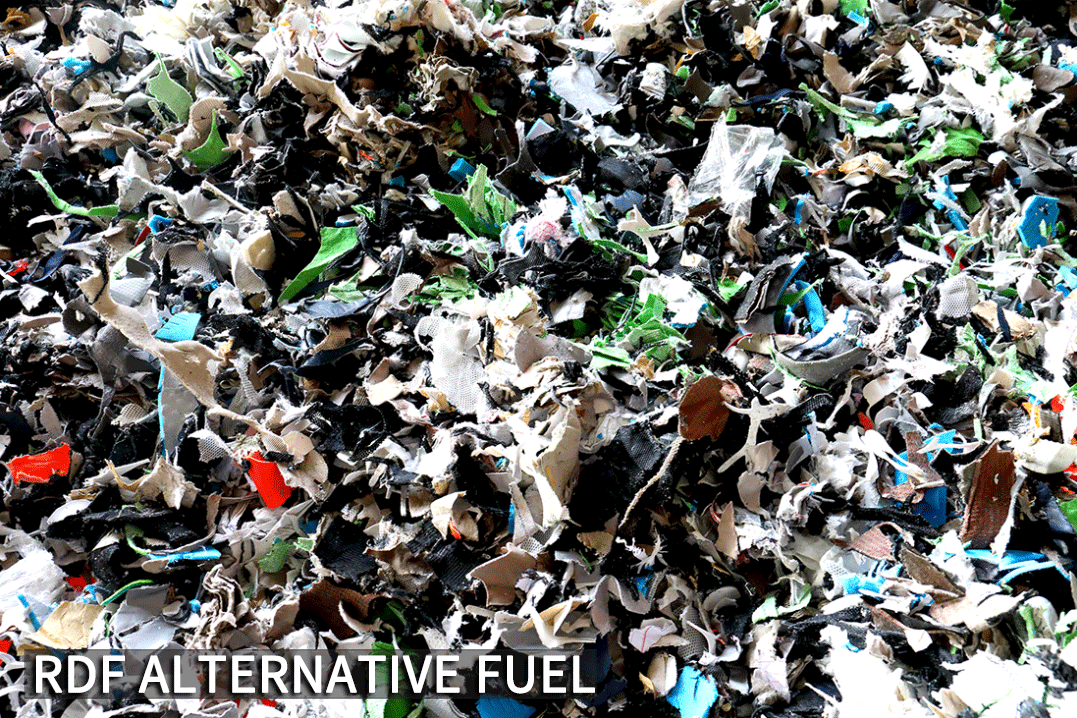
Facing the market situation of high movement for the coal price at now, the fluctuating fuel cost is a big challenge for many coal-fired enterprises.
As mentioned above, this cement company finally adopted the way that RDF alternative fuel is processed from all kinds of solid waste, to control its fuel costs efficiently.
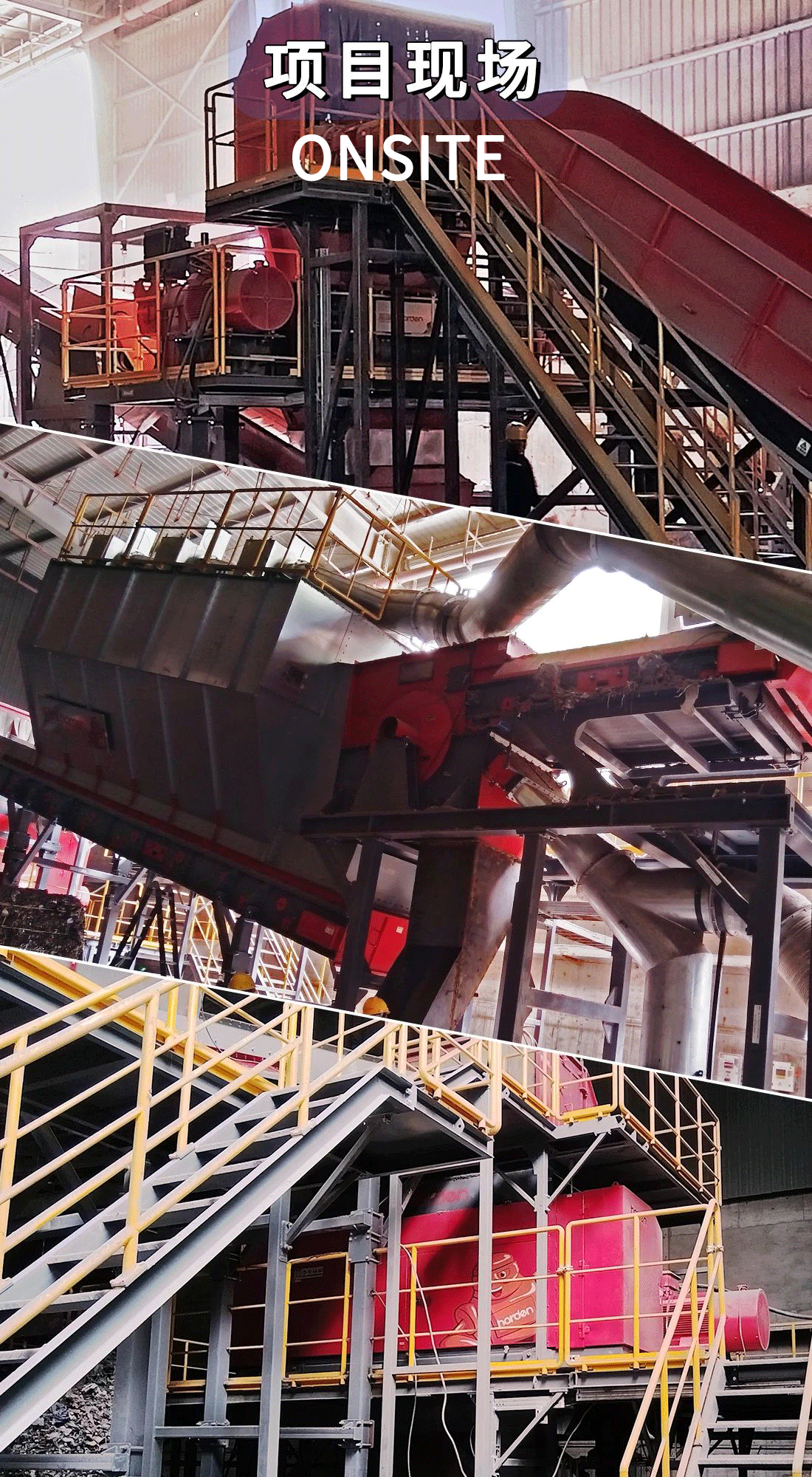
This cement industry has cooperated with Harden Machinery Ltd., which has deeply specialized in the solid waste processing industry for more than 14 years. We discussed and practiced focusing on the “Solid Waste RDF Alternative Fuels.
From solid waste supply situation to cost benefits analysis, from raw materials to RDF alternative fuel processing flow, from fuels’ capacity/ calorific value to stability of cement kiln, after we had fully considered multiple information, finally our customer determined to apply Harden DWS alternative fuel preparation system.
This system adopted the “primary shredder, magnetic separator, wind shifter, fine shredder” with multiple solid waste processing technologies, promising the whole capacity could reach 200 tons per day.
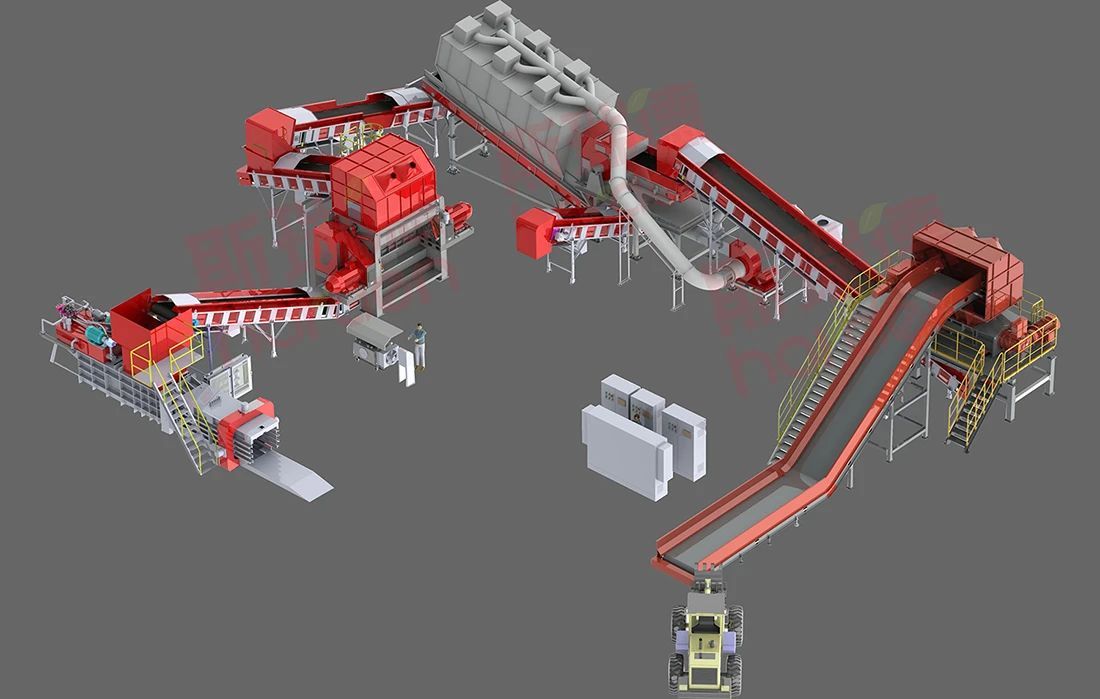
It processed the various solid waste such as waste leather, textile, and plastic into a high calorific value RDF alternative fuel with an impurity content of less than 10%, a high degree of homogenization, and a discharge size of about 50mm.
With Harden RDF alternative fuel preparation technologies, these industrial solid wastes are prepared into high calorific value RDF alternative fuel. It has fewer harmful elements and a lower heat loss coefficient when burned in the kiln.
It has less impact on cement kiln fluctuations and cement quality and meets the requirements. The demand for continuous and stable large-scale application of "RDF alternative fuel" to replace "fossil fuels such as coal" in cement kilns.
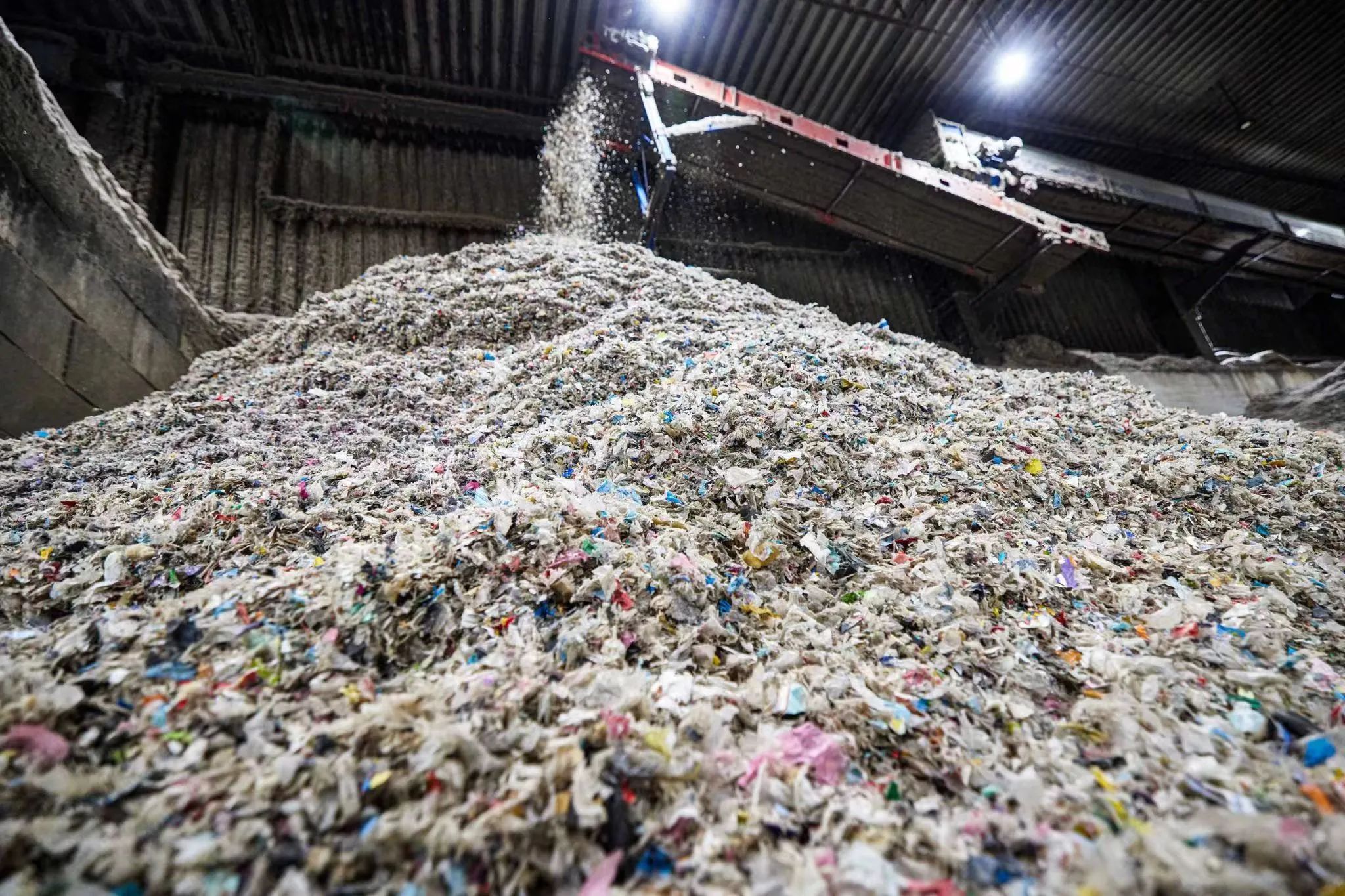