Cement companies with RDF alternative fuel preparation system will seize the opportunity!
Mainstream Carbon Reduction Methods
In the cement clinker production process, industrial process emissions account for about 60%-65%, mainly carbon dioxide emissions produced by the decomposition of carbonates.
Emissions from energy activities account for about 35%-40%, mainly carbon dioxide emissions produced during the combustion of fossil fuels such as coal.
Also, the indirect emissions from the use of electricity are not included in carbon emissions.
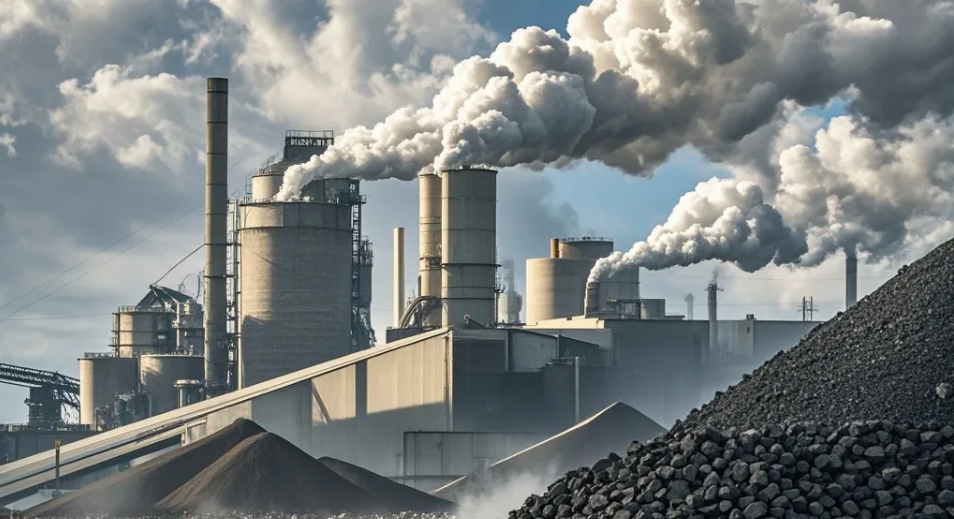
In terms of emission proportion, the cement industry’s reduction in process carbon emission intensity means finding raw materials to replace carbonates such as limestone, but this is very difficult.
Therefore, by reducing the use of fossil fuels and increasing the proportion of clean energy blends, the use of RDF alternative fuels has become a mainstream way to reduce carbon emissions.
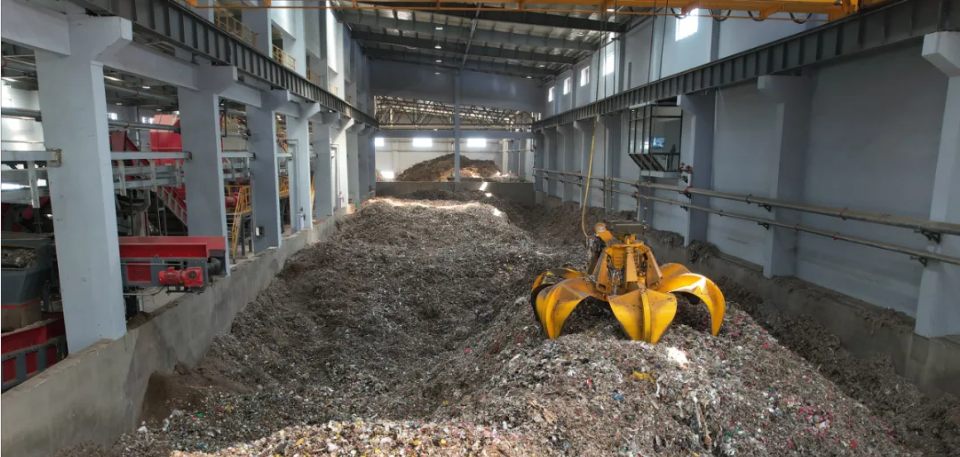
RDF alternative fuel preparation technology
Harden Machinery Ltd. has been deeply involved in the solid waste treatment industry for more than ten years.
It has conducted multiple experiments on the current mainstream RDF raw materials, such as waste cloth, leather scraps, waste plastics, paper mill light residue, and other materials with different flexibility and humidity. Continuously improve and optimize equipment around the demand for fuel entering the kiln.
Based on the concept of "Just Shred it, Thus Sort it", the industrial solid waste RDF preparation system compatible with various solid wastes has been launched.
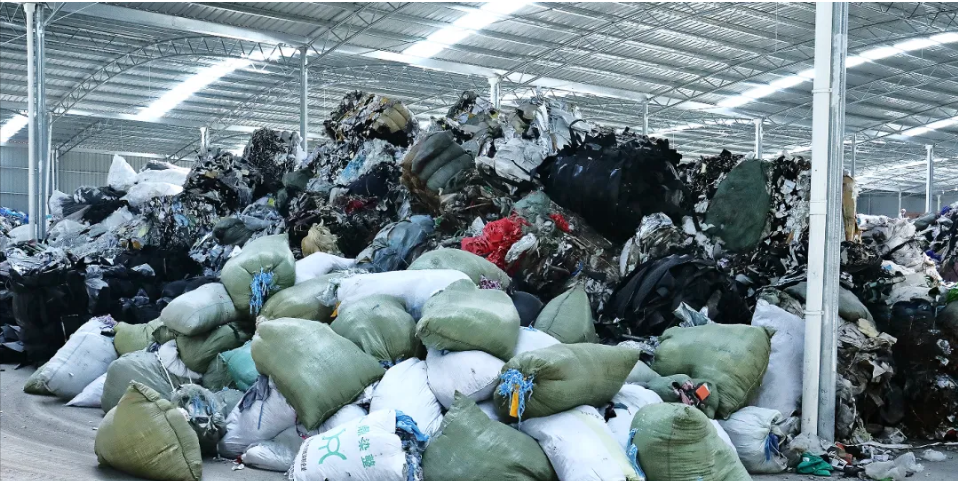
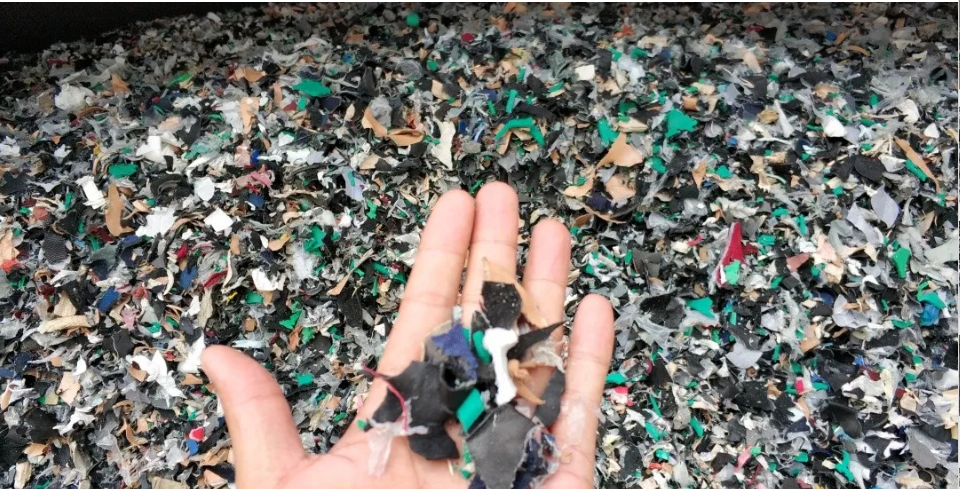
From the perspective of global development, the carbon market can give full play to the decisive role of the market in resource allocation, thereby cement companies equipped with RDF preparation system will get benefits from this.